INTRODUCING DIGITAL ASSET MANAGEMENT
The key to increasing profit and productivity in your business
90
Hours
spent searching
On average, 90 hours a month are spent searching for assets across construction sites.
65
%
difficulties with tracking
65 per cent of customers have trouble keeping track of required certificates and maintenance dates.
56,000
$ AUD
wasted every year
On average, AUD 56,000 are spent annually searching for assets.
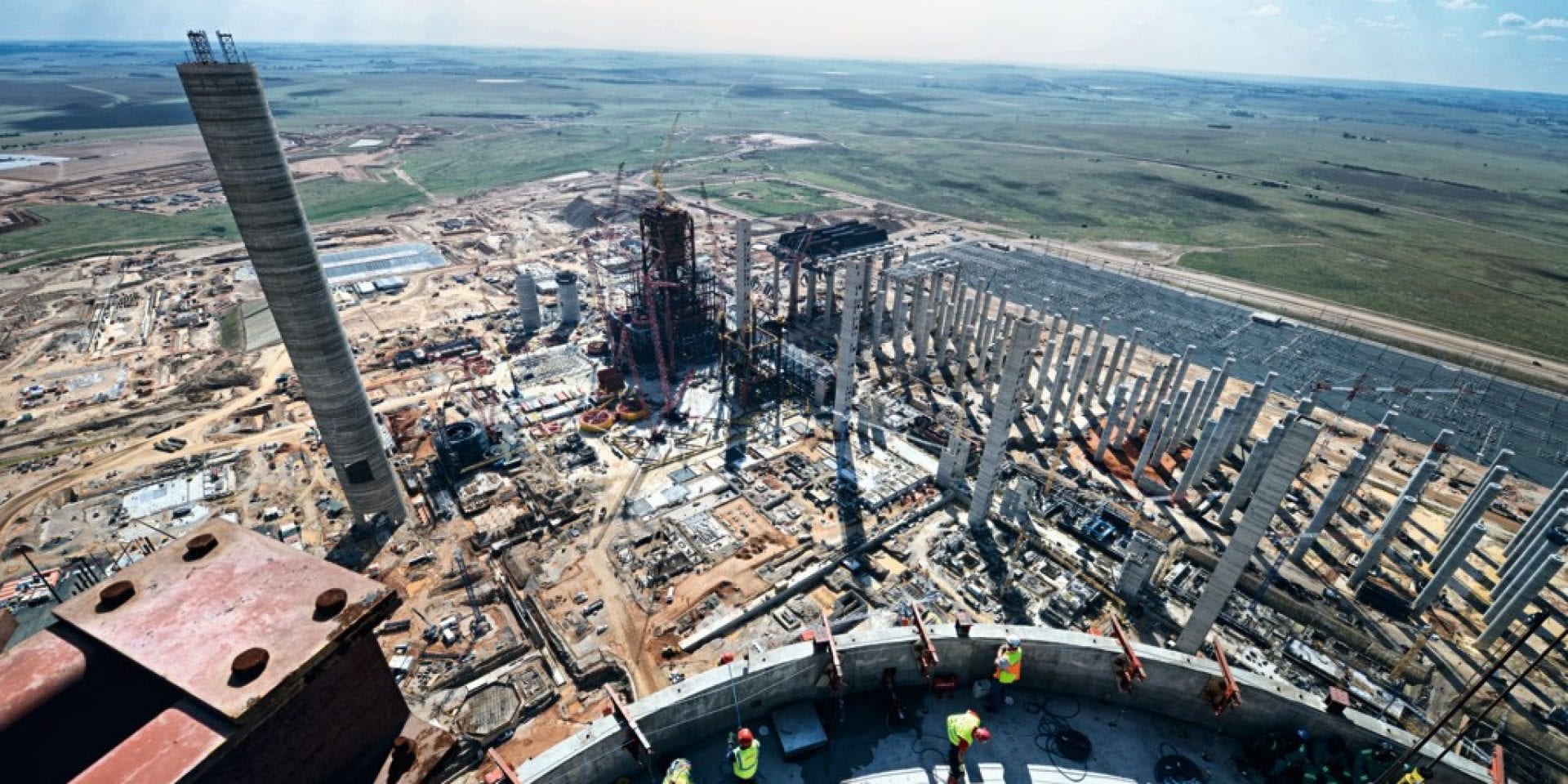